Glass production requires high-temperature furnaces, which rely on refractory materials. Optimizing furnace lifespan and efficiency is crucial for the glass industry. Kerui offers suitable glass furnace refractory package solutions to meet these needs. We have partnered with leading glass manufacturers like Pilkington, Xinyi Glass, and AGC Inc.
Introduction of Common Refractory Materials in Glass Furnace
Industry | Refractories | Types of Furnace | Use Area |
---|---|---|---|
Glass | Part 1. Refractory Bricks: -Silica Bricks; -AZS Bricks; -High Alumina Bricks; -Magnesia Chrome Bricks; -Magnesia Bricks; -Sillimanite Bricks; -Low Creep Clay Bricks; -Zirconium Oxide Bricks; -Zirconium Corundum Bricks; -Alumina Silicate Bricks; -Silicon Carbide Bricks; -Synthetic Spinel Bricks; -Magnesium Aluminate Spinel Bricks; -Synthetic Magnesia Aluminate Spinel Bricks; Part 2. Insulation Refractories: -Insulation Bricks; -Ceramic Fiber Products; | Float Glass Production Line; Glass Melting Furnace; Tempering Furnace; Rotary Kiln; Glass Fiber Melting Furnace; Rolling Furnaces; | Bath And Cooling Area; Quenching Furnace; Furnace Bottom; Furnace Wall; Regenerator; Kiln Roof; Flue. |
List of Common Refractory Materials in Glass Furnace – Refractory Bricks
Silica Bricks for Glass Furnace
Silicon brick is a commonly used refractory material in glass furnaces. It has a SiO2 content of over 94% and a bulk density of less than or equal to 2.35.
- Characteristics: High-temperature resistance, excellent chemical corrosion resistance, good thermal stability, and good dimensional stability.
- Applications: It is primarily used in the molten pool crown, melting tank, regenerator, and flue.
- Precautions: It has poor impact resistance and a high coefficient of thermal expansion. When laying bricks, appropriate expansion joints should be left.
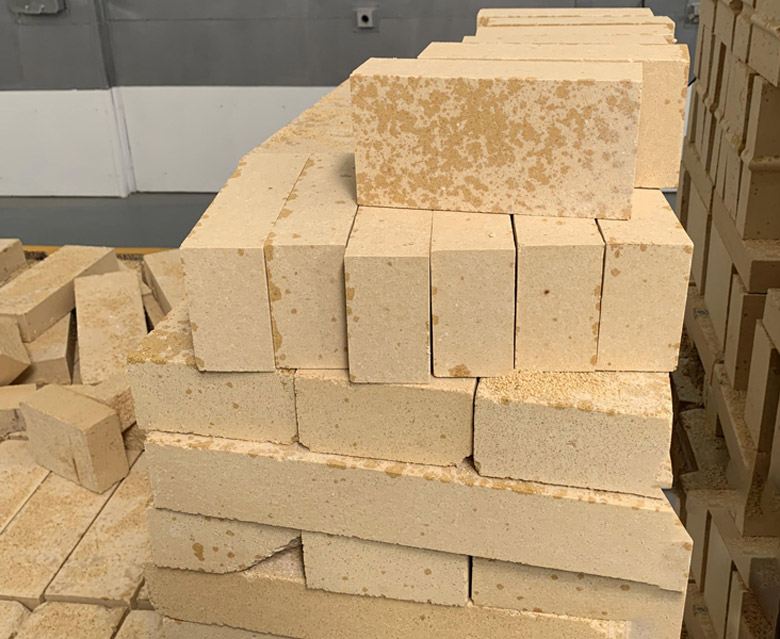
AZS Bricks for Glass Furnace
AZS brick is highly resistant to the harsh working conditions of glass furnaces, making it a widely used refractory material. It is produced by mixing select zircon sand and industrial alumina powder in specific proportions. The SiO2 content exceeds 12%, and the ZrO2 content is greater than 33.5%.
- Characteristics: High-temperature resistance, excellent alkali corrosion resistance, strong wear resistance, good thermal stability, and superior thermal shock resistance.
- Applications: It is commonly used in the construction of glass melting pools, furnace walls, furnace bottoms, forehearths, batch houses, and throat bricks. This type of brick can withstand prolonged chemical erosion from molten glass. Additionally, it is highly resistant to long-term mechanical abrasion and erosion caused by liquid flow.
- Precautions: Due to thermal expansion, appropriate expansion joints should be left during installation.
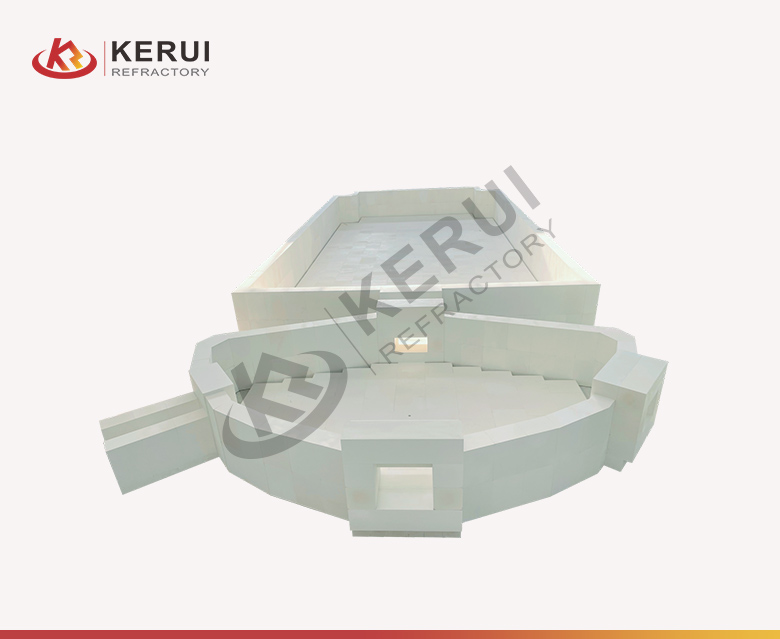
Magnesia Chrome Bricks for Glass Furnace
Magnesia chromite brick typically contains 45-65% MgO and 8-16% Cr2O3. Its refractory temperature ranges from 1530°C to 1650°C.
- Characteristics: High melting point, excellent thermal shock resistance, alkali resistance, and high mechanical strength.
- Applications: Used extensively in regenerators, furnace bottoms, furnace walls, forehearths, and other high-temperature areas. This brick can withstand prolonged immersion in molten glass and high-temperature shocks.
- Precautions: To mitigate thermal stress, it is recommended to combine magnesia-chromite bricks with other refractory materials.
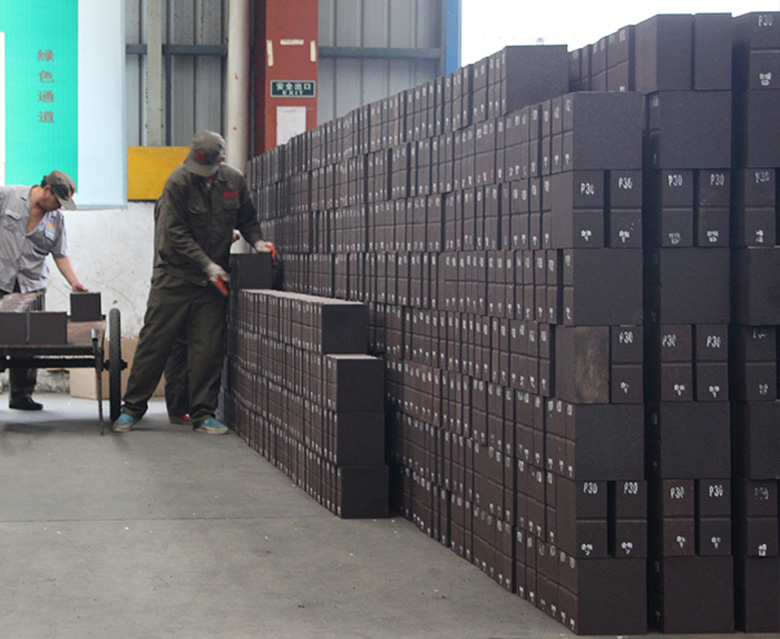
Magnesia Bricks for Glass Furnace
Magnesia chromite brick typically contains 91.5-97.5% MgO. Its refractory temperature ranges from 1560°C to 1700°C.
- Characteristics: High melting point, excellent thermal shock resistance, alkali resistance, and high mechanical strength.
- Applications: Used extensively in regenerators, furnace bottoms, furnace walls, forehearths, and other high-temperature areas. This brick can withstand prolonged immersion in molten glass and high-temperature shocks.
- Precautions: To mitigate thermal stress, it is recommended to combine magnesia bricks with other refractory materials.
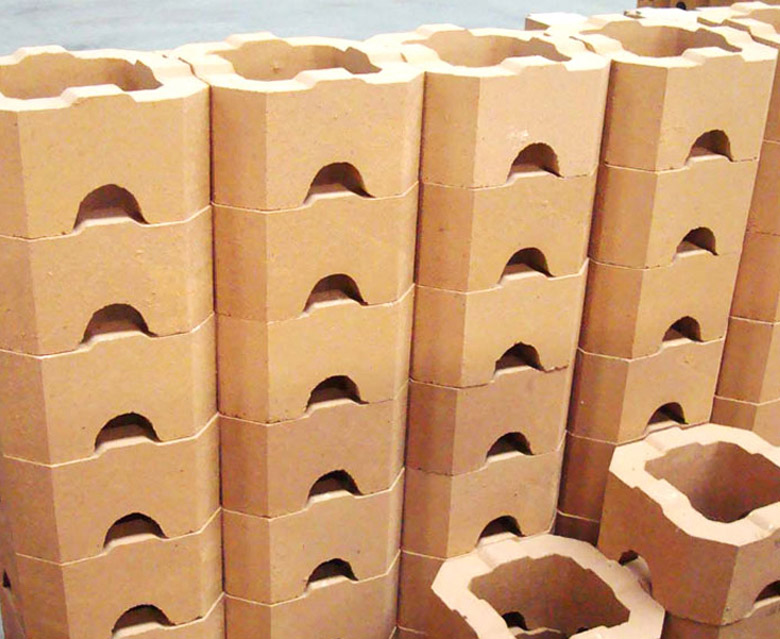
Sillimanite Bricks for Glass Furnace
Sillimanite brick typically contains 50-62% Al₂O₃ and 32-37% SiO₂. Its refractory temperature ranges from 1600°C to 1650°C.
- Characteristics: High refractoriness, excellent thermal shock resistance, strong chemical corrosion resistance, and good dimensional stability.
- Applications: Commonly used in the tail of the molten pool, batch house, feeder, crown, and walls of glass furnaces.
- Precautions: To prolong service life, operators should carefully control furnace temperature, load, and atmosphere.
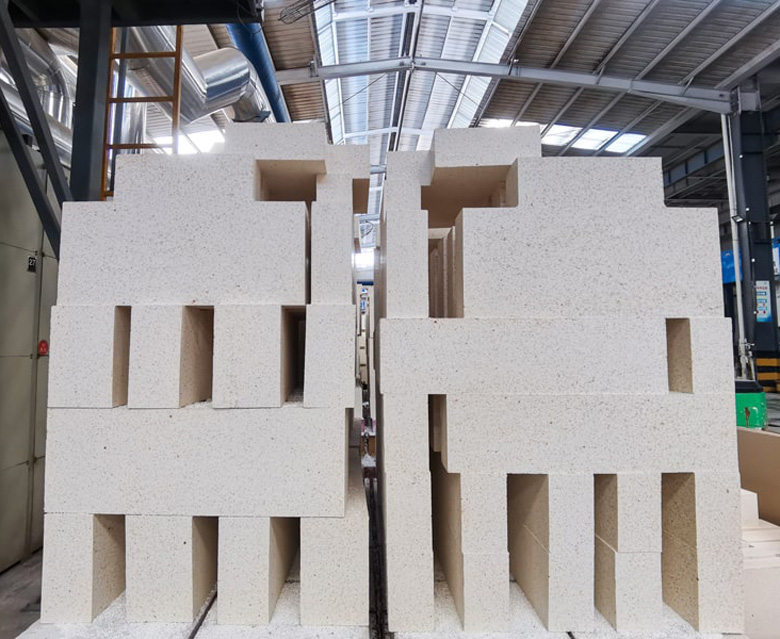
Low Porosity Clay Bricks for Glass Furnace
Low-porosity fireclay brick is a traditional refractory material. Its Al₂O₃ content ranges from 30% to 45%, and its refractoriness is between 1250°C and 1420°C.
- Characteristics: Low porosity, high density, low cost, high refractoriness, strong acid corrosion resistance, and good wear resistance.
- Applications: Commonly used in the tin bath, furnace bottom, walls, and regenerators of glass furnaces.
- Precautions: This type of brick has relatively poor thermal shock resistance when used in glass furnaces.
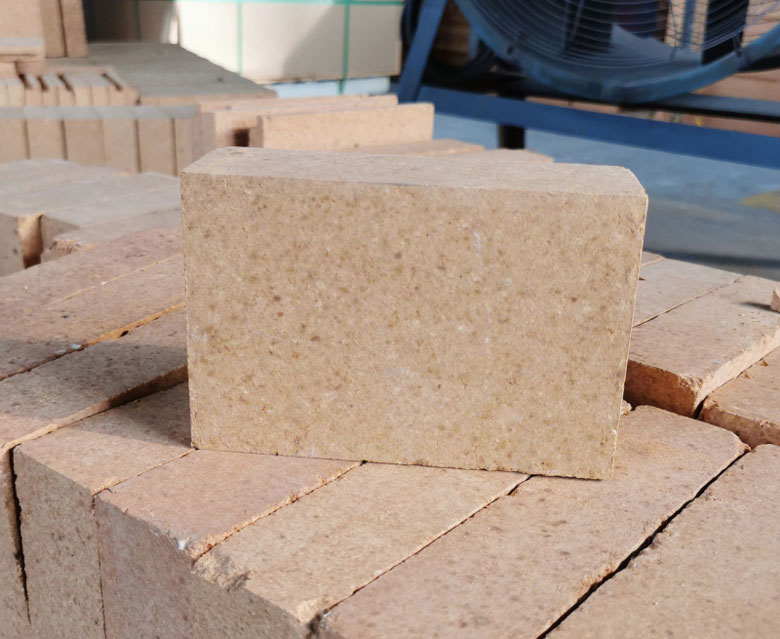
High Alumina Bricks for Glass Furnace
High-alumina brick typically contains 48-80% Al₂O₃ and has a refractory temperature ranging from 1420°C to 1530°C. The alumina bricks and fused alumina bricks are available.
- Characteristics: High temperature resistance, excellent thermal shock resistance, strong chemical corrosion resistance, and high strength.
- Applications: Commonly used in the flue, lower regenerator lining, furnace bottom lining, crown, and walls.
- Precautions: High-alumina bricks have good resistance to acidic atmospheres but are relatively weaker against alkaline atmospheres.
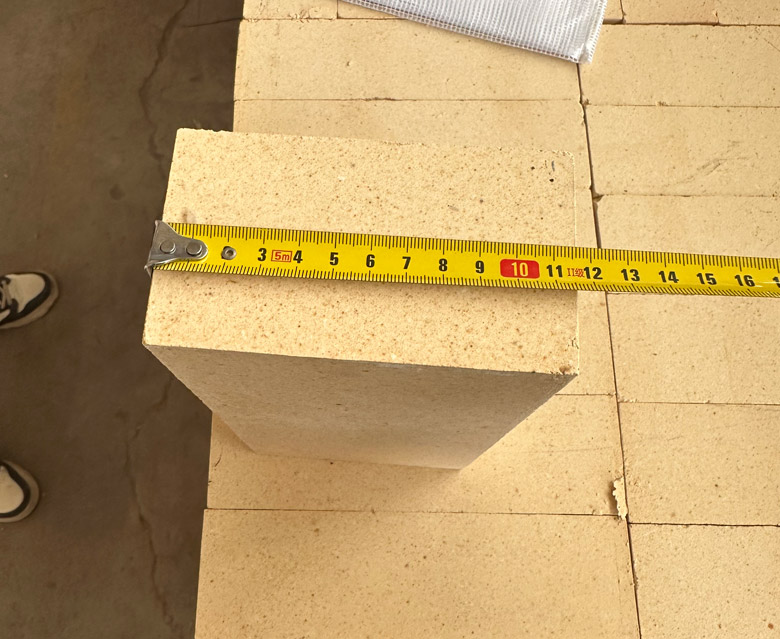
Magnesia Spinel Bricks for Glass Furnace
Magnesia spinel brick has above 30% of Al₂O₃ content. And its refractoriness is between 1250°C and 1650°C.
- Characteristics: High temperature resistance, good thermal shock resistance, high strength, corrosion resistance.
- Applications: Furnace bottom and walls, regenerator, kiln roof, etc.
- Precautions: Before installation, magnesia spinel bricks should be kept dry and avoid long-term storage in a humid environment.
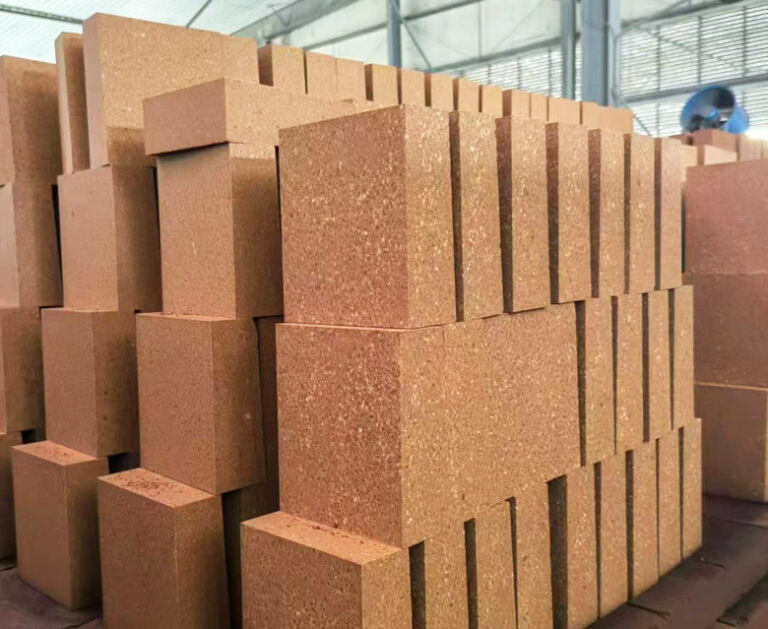
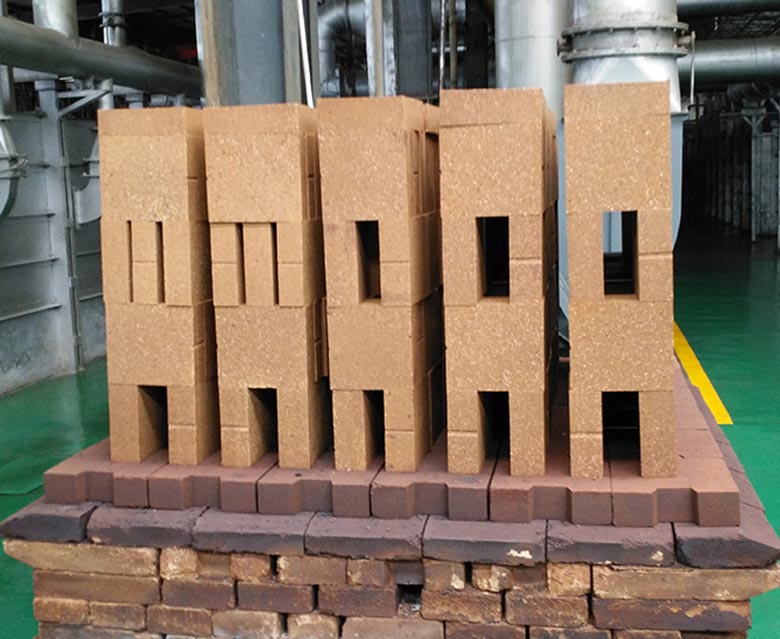
Silicon Carbide Bricks for Glass Furnace
Silicon carbide brick has above 85% of SIC content. And its refractoriness is between 1250°C and 1750°C.
- Characteristics: High temperature resistance, good thermal shock resistance, high strength, asicd corrosion resistance.
- Applications: Kiln bottom and wall, heat storage chamber, kiln roof, material channel, etc.
- Precautions: Before installation, magnesia spinel bricks should be kept dry and avoid long-term storage in a humid environment.
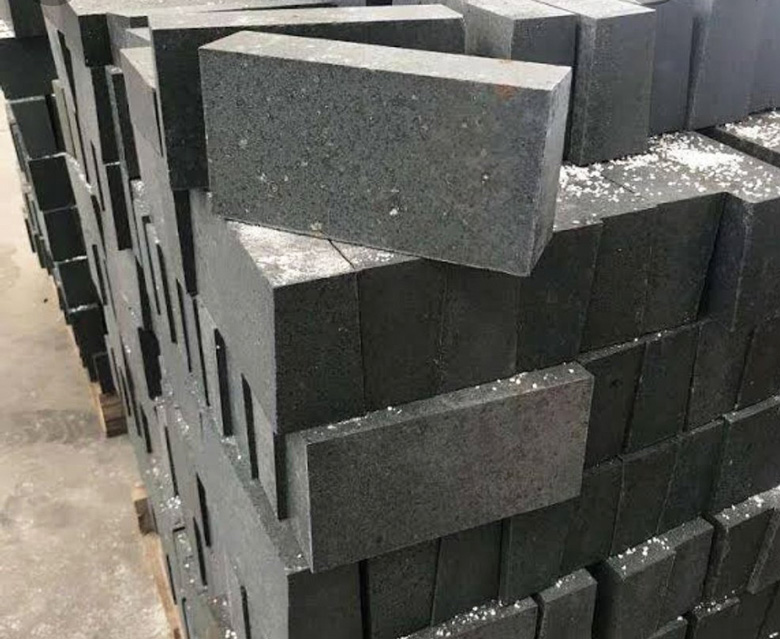
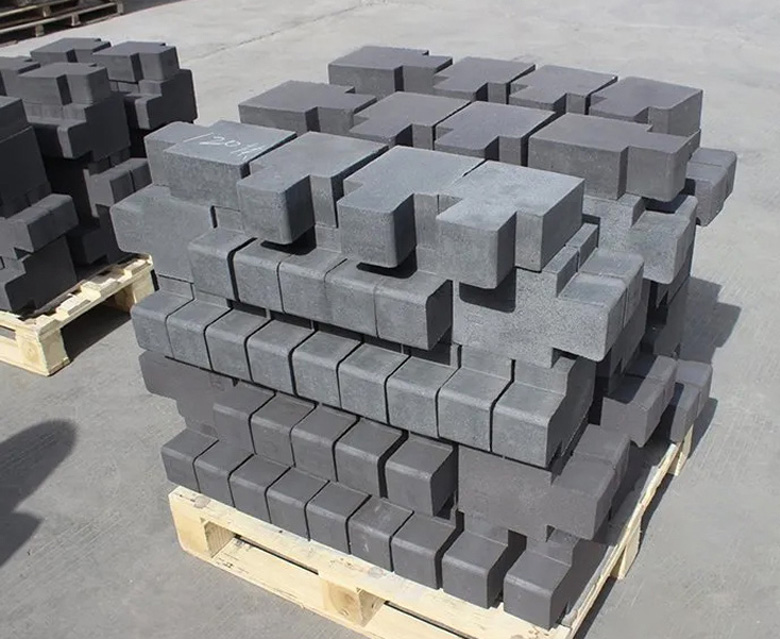
List of Common Refractory Materials in Glass Furnace-Refractory Bricks – Insulation Refractory Products
Ceramic Fiber Products for Glass Furnace
Ceramic fiber products typically contains 39-55% Al₂O₃ and has a classification temperature between 1050°C and 1430°C.
- Characteristics: High temperature resistance, excellent thermal insulation, strong thermal shock resistance, good chemical stability, and high flexibility.
- Applications: They are commonly used for Kiln roof insulation, melting insulation layer, furnace shell insulation, piping, furnace door seals, furnace linings, furnace roofs, high-temperature thermal barriers, burners and pipe insulation, seals, and high-temperature filters, expansion joint filling, thermal expansion compensation, and so on.
- Precautions: Pay attention to the operating temperature and installation method.
Calcium Silicate Boards for Glass Furnace
Calcium silicate board typically contains 46-48% SiO₂ and 39-41% CaO. Its operating temperature is below 1000°C.
- Characteristics: High-temperature resistance, excellent thermal insulation, strong thermal shock resistance, good chemical stability, high hardness, and good machinability.
- Applications: Commonly used in the kiln wall insulation, outer shell of glass furnaces, furnace roof insulation, furnace inspection openings, and furnace ducts.
- Precautions: Pay attention to the operating temperature and installation method.
Solutions and Services Kerui Refractory Provides for Glass Furnace
Kerui Refractory tailors refractory material selection plans for clients based on factors such as kiln type, production process, and glass type.
- Solutions: Professional team provides you with the best refractory solution for glass furnaces based on your furnace conditions;
- Products: Customized refractory products and refractory performance analysis for glass furnaces;
- Design: Customized glass furnace refractory design drawings;
- Delivery: Best shipping route solution and container solution;
- Logistics: Real-time updates on refractory product logistics information;
- Construction: Construction guidance at the local site;
- Technical guidance: Kerui Refractory provides maintenance recommendations, preventive maintenance plans, and wear reduction solutions. We offer quick response and supply services to our customers.
Through our continuous innovation and service upgrades, Kerui Refractory‘s products have demonstrated excellent performance in the operation of glass furnaces. Our partners have given us positive evaluations. Kerui is ready to join you in meeting the various challenges in the glass industry! We will continue to break through our own limits and bring more efficient and high-value refractory materials and solution services to our partners!