Refractory bricks play a pivotal role in thermal containment environments. Their inherent safety and performance enable them to function effectively under extreme temperature conditions. Unlike ordinary bricks, refractory bricks exhibit exceptional resistance to cracking or performance degradation under high temperatures and mechanical stresses. Consequently, they are indispensable components in high-temperature applications. Kerui Refractory mainly provides the following 9+ types.
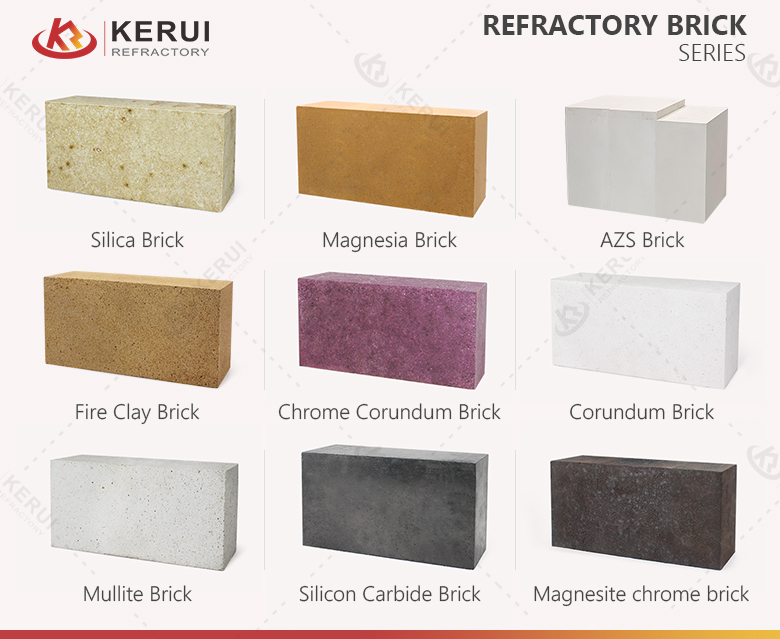
What Are Refractory Bricks?
Refractory bricks are specialized construction materials designed to withstand extreme heat and harsh environments. They are typically composed of a blend of refractory materials, mineral substances, and other raw ingredients. They are processed through various manufacturing techniques. These bricks are characterized by their exceptional refractoriness, chemical corrosion resistance, and ability to endure thermal shock.
What is the Refractory Brick Made of?
Refractory bricks China are composed of a blend of raw materials, each contributing specific properties to the final product. These materials can be broadly categorized into the following groups: Alumina (Al2O3), Magnesia (MgO), Silica (SiO2), Chrome Ore (Cr2O3), Zircon (ZrSiO4), Magnesite Dolomite (MgCO3•CaCO3), clay, other raw materials. These refractory materials have different physical and chemical properties, such as refractoriness, flexural strength, load softening temperature, thermal conductivity, thermal shock resistance, and so on. Therefore, they are used in the production of various refractory bricks.
What Is the Manufacturing Process of Refractory Bricks?
Different usage scenarios have different performance requirements for refractory bricks. Therefore, in order to meet the needs of various scenarios, Kerui Refractory will produce different refractory bricks according to the following processes.
- Pressing: Manufacturing equipment presses the raw materials into refractory bricks.
- Sintering: After the raw materials are pressed into bricks, the bricks are sintered and formed at high temperatures.
- Electric melting: The raw materials are melted in an electric arc furnace. The they are poured into molds, and cooled to form refractory bricks.
What Are the Benefits of Refractory Bricks?
The refractory bricks have many advantages. These features make they be used in high-temperature environments that meet the usage requirements.
- High refractoriness;
- Resistance to chemical corrosion;
- Thermal shock resistance;
- Low thermal conductivity;
- Abrasion resistance;
- And so on.
What Factors Affect the Performance of Refractory Bricks?
There are many factors to affect the performance of refractory bricks. The factors mainly include the quality of raw materials, composition, content, manufacturing process, and so on. As a refractory material manufacturer and refractory solution expert, Kerui Refractory can develop special refractory materials based on the application scenarios of our partners.
What are Refractory Bricks Used for?
- Steel industry;
- Non-ferrous metal industry;
- Glass industry;
- Cement industry;
- Ceramic industry;
- Electrical industry;
- And so on.
Refractory bricks are classified into over 30 types based on their composition and manufacturing processes, for example, AZS refractory brick. Kerui Refractory is a specialist in the field of refractory materials. We offer a wide range of kiln design solutions and refractory product combinations. If you have any requirements in this regard, please contact us.