Kerui Refractory completed an upgrade of its high-grade refractories plant In May 2025. This is one of our refractory factories in Xinmi, Zhengzhou, Henan, China. This upgrade enhances the production of ultra-high temperature special refractories. These materials withstand temperatures over 1700°C. The upgrade uses intelligent equipment and process innovation. It addresses material demands in metallurgy, glass, and hazardous waste treatment industries. These industries operate under harsh conditions.
The Upgrade of Kerui High-grade Refractories Plant
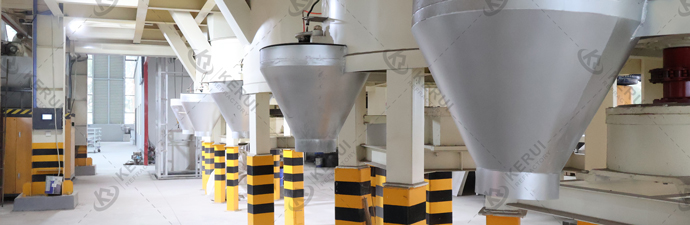
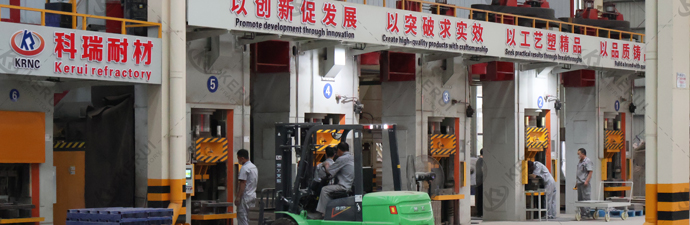
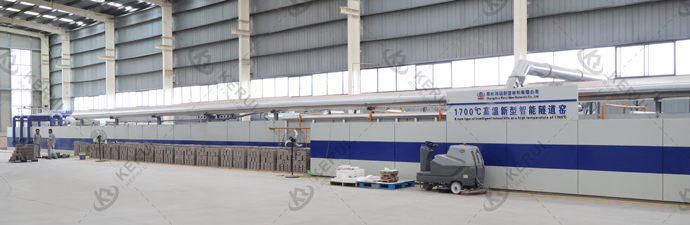
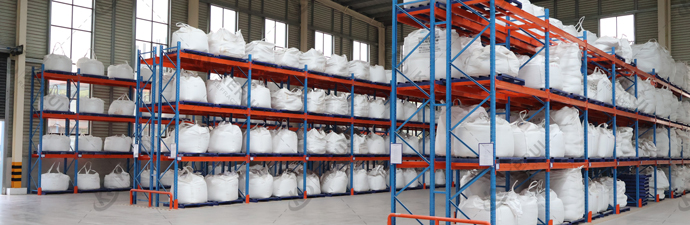
The Range of Kerui High-end Refractory Products
Part.1 Refractory Bricks
High-grade Refractory Bricks | Features |
Corundum Mullite Bricks | Excellent thermal shock resistance |
Sintered Corundum Bricks | Extremely high temperature strength |
Zircon Bricks | Strong resistance to glass liquid erosion |
Chrome Corundum Bricks | Outstanding resistance to slag penetration |
Chrome Corundum Bricks | Phase change toughening and anti-stripping |
Sillimanite Bricks | Low thermal expansion coefficient, resistance to thermal stress cracking |
Alumina Hollow Ball Bricks | Low thermal conductivity, operating temperature>1800℃ |
Part.2 Refractory Castable Casting Material
Refractory Castable | Features |
Corundum Castable | Good self-flow performance, strong high temperature volume stability |
Chrome Corundum Castable | Resistance to molten metal penetration, resistance to acid slag erosion |
Silicon Carbide Castable | High thermal conductivity, resistance to aluminum liquid wetting |
Customization Capability Breakthrough of High-grade Refractories
- Micro-batch Production: Double shuttle kilns enable precision firing (±5°C) for niche orders like special-shaped bricks.
- Harsh-condition Adaptation: Manufacturing equipment auto-optimizes parameters for special refractories, including Auto batching system, adaptive presses, mold, and others.
Kerui Offers Furnace Lining Solutions Upgrade
Kerui delivers comprehensive kiln lining solutions tailored to customers’ needs, covering extreme-condition applications from metallurgy to hazardous waste processing.
- Full Life Cycle Design: One-stop service for pre-diagnosis of working conditions and optimization of material matching.
- Industry-specific Solutions: Customized solutions for different industries and different working conditions.
- Smart Construction Support: Modular prefabricated parts and monitoring of refractory castable rheological properties.
- Extreme Performance Guarantee: A variety of high-end refractory products are supplied to ensure good kiln operation performance.
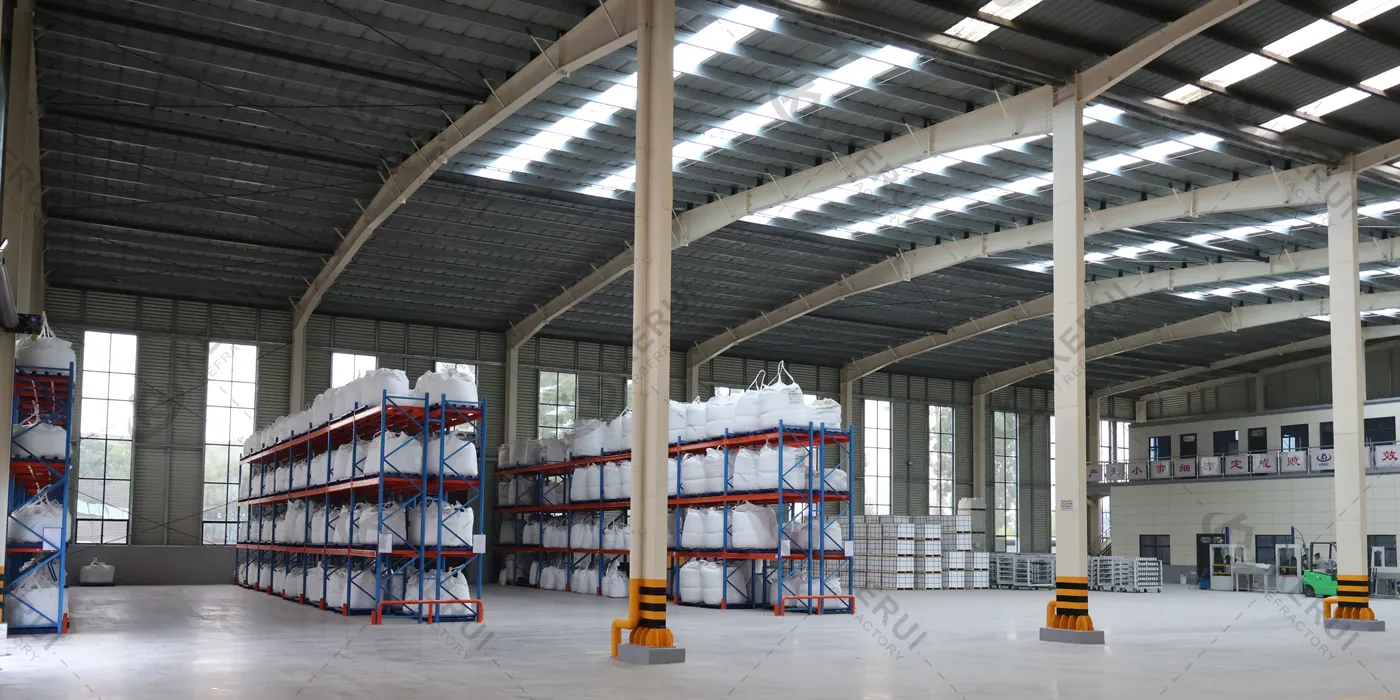
High-end Refractories for Critical Industrial Processes
Partner with Kerui Refractory
Kerui provides ISO 9001 certified refractory solutions. With 20 years of ultra-high temperature expertise, we developed 37 patented technologies. Our adaptive pressing systems deliver precision within ±5°C. Kerui materials reliably perform in extreme conditions over 1700°C. We serve 2,000+ global clients across metallurgy, glass and hazardous waste sectors. Industry leaders like RUSAL trust our solutions through lasting partnerships. Contact us today for your needs.