The steel industry is a fundamental industry of every country. The infrastructure of countries is closely linked with the development of the steel industry. However, in the development progress, we cannot ignore the pollution of the steel industry. Selecting the optimal refractories can extend the service time of equipment and reduce pollution.
Introduction of Steel Furnaces
The steel industry mainly uses blast furnaces and converters to make iron and steel. Blast furnaces produce slag, melted iron, and chemical gases except the iron. Converters will blow air or gases into equipment and release exhaust fumes. In this situation, the refractories used in steel furnaces must have high refractoriness, stable chemical structure, and good thermal shock resistance.
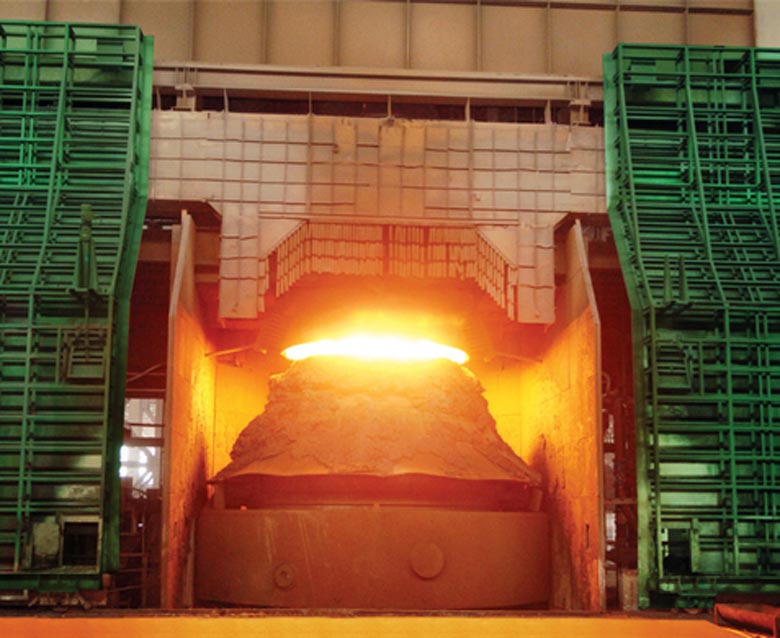
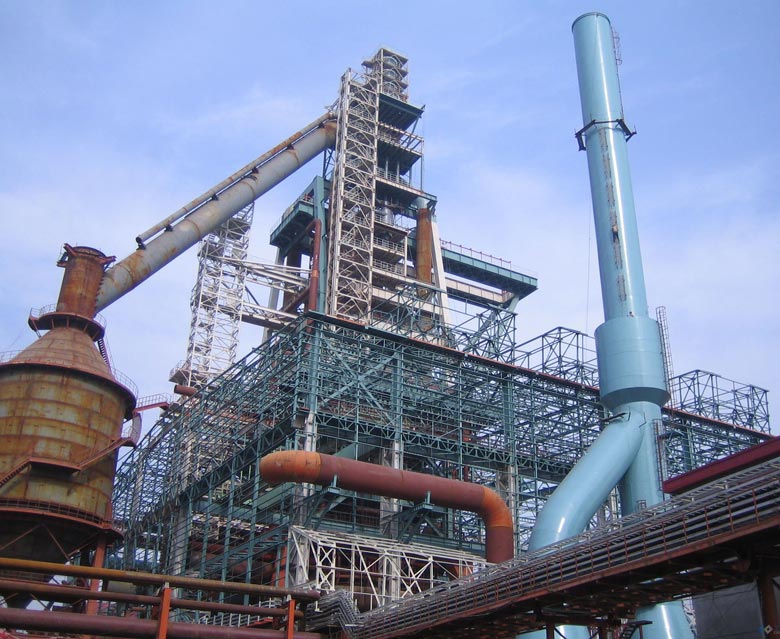
Refractories Used in Steel Industrial Equipment
Blast furnaces can be divided into three parts: the top, the middle, and the bottom.
- At the top of blast furnaces, the raw materials and the chemical gases will erode the linings. These parts need to resist material erosion and thermal shock. So high-density fire clay bricks and high alumina bricks are suitable refractory bricks for the linings.
- The middle part is the working layer. It will erode by different substances, including alkaline metals, chemical steam, thermal shock, and carbon slag. So this part mainly uses high alumina refractories, corundum mullite bricks, and silica carbide bricks.
- Carbon bricks and silica carbon bricks are used for the bottom of blast furnaces. Silica carbon bricks have a low thermal expansion coefficient. So they can resist the extreme temperature that keeps steady structures.
The refractories of converters usually use alkaline materials. Magnesia carbon bricks, dolomite bricks, and magnesia bricks can used for the linings of working layers. They can resist chemical slag erosion and thermal shock. In the extreme temperature change, they also can keep a steady state.
Some converters also use acidic materials as the linings. Mullite bricks and corundum bricks can resist acidic materials and slag erosion. They can used for the lining and bottom.
Senior Refractory Expert
Kerui has abundant experience in the refractory industry. We are devoted to providing more innovative solutions for every customer. Kerui has more than 18 patents for refractory products. We are devoted to contributing to the development of the global high-temperature industry.
Outstanding Consultant Team
Kerui has professional consultant teams to solve questions from customers. They not only help customers select suitable sizes of bricks but also can recommend the optimal refractory bricks for different industrial high-temperature equipment. Kerui guarantees that our consultants have professional training.