The development of the chemical industry can affect the state economy. The chemical industry is an important part of the state economy that involves many fields. So many countries focus on the sustainable development of the chemical industry. Refractory materials used in the chemical industry are no exception.
Introduction of Chemical Industry
The chemical industry includes three parts: petrochemical, basic chemical, and chemical fiber industry. The common high-temperature equipment includes synthetic ammonia conversion furnaces, carbon black reaction furnaces, coke ovens, carbon furnaces, and pyrite roasting furnaces.
Refractory Materials Used for Chemical Industry
Synthetic ammonia conversion furnaces usually use the alumina bubble castable as the linings refractory products. Alumina bubble castable can resist strong thermal shock. The bottom uses corundum bricks.
Carbon black reaction furnaces can use corundum bricks, alumina bubble bricks, and castable. The linings of furnaces use high-purity corundum bricks to resist thermal shock and chemical erosion. The outer layers use the alumina bubble castable. The insulation layers use light insulation castable.
Coke ovens and carbon furnaces can use silica bricks, clay bricks, high alumina bricks, insulation bricks, and castable. Silica bricks are used for the linings of coke ovens and carbon furnaces. They can resist the chemical erosion. Clay bricks are used for the linings of flue and regenerative chamber checker bricks. High alumina bricks are used for the head position of coke ovens.
Pyrite roasting furnaces use high alumina bricks and clay bricks as the linings of furnaces. They can resist the high-temperature environment and keep a stable volume.
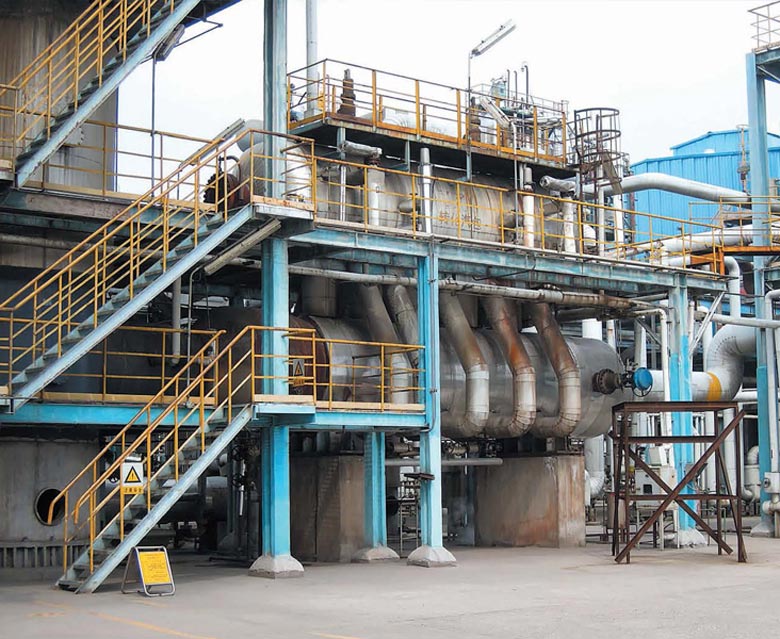
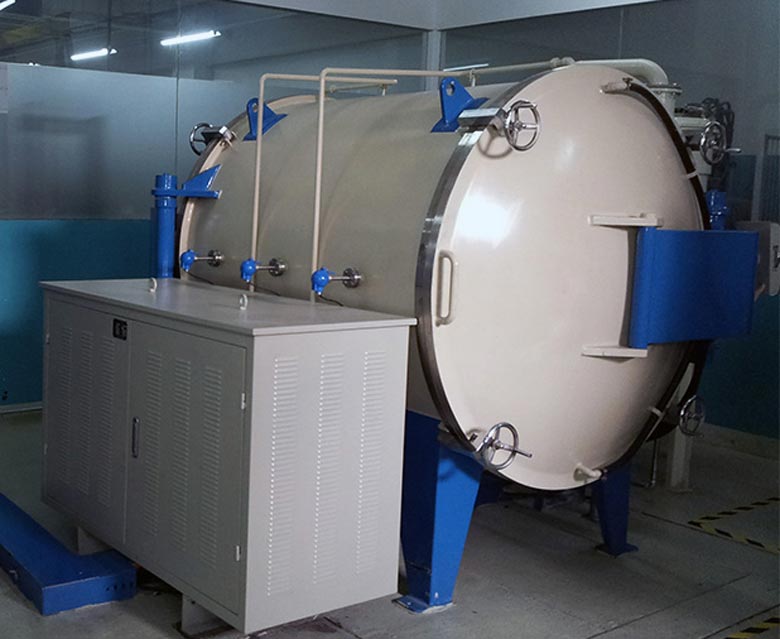

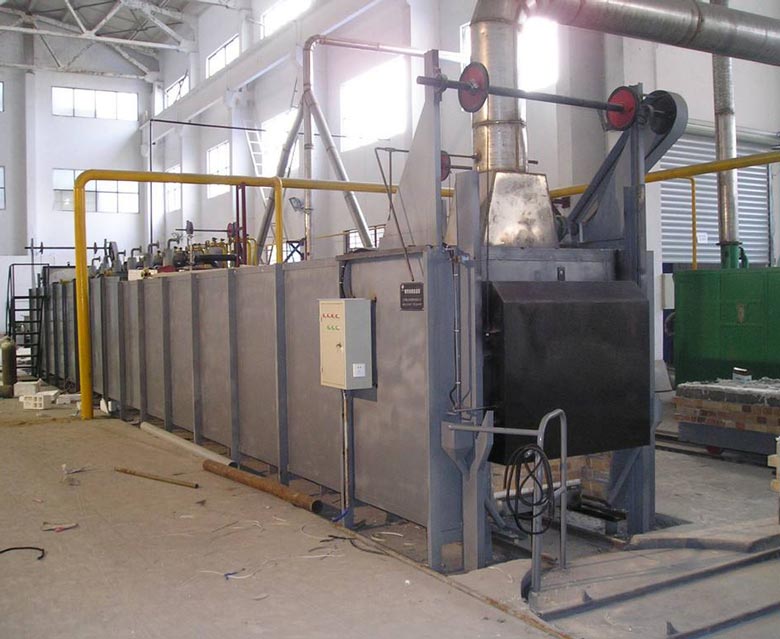