There are significant differences in composition and application scenarios between mullite bricks and mullite insulating bricks. We are a comprehensive group enterprise that integrates the production and sales of refractory materials, product technical solutions, and project EPC general contracting services. The mullite insulating bricks we produce are exported to dozens of countries, including Ukraine, Singapore, South Korea, and Lebanon.
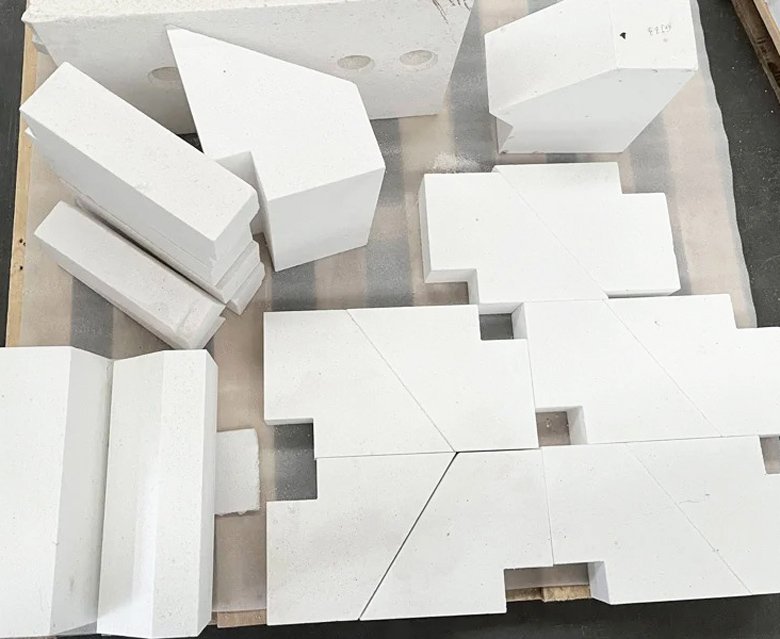
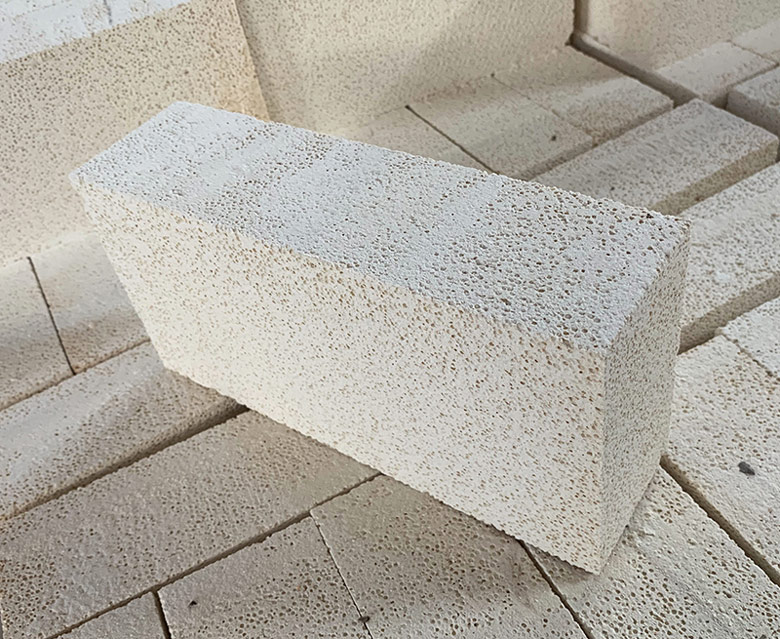
Differences Between Mullite Brick And Mullite Insulation Brick
Mullite bricks and mullite insulating bricks mainly differ in the following aspects:
1. Composition and Definition
Mullite Bricks: These are high-alumina refractory materials primarily composed of mullite as the main crystalline phase, with an alumina content typically ranging from 65% to 75%. In addition to mullite, they may also contain a glass phase, quartz (when the alumina content is lower), or corundum (when the alumina content is higher).
Mullite Insulating Bricks: These are refractory materials with excellent thermal insulation properties, usually achieved by introducing pores or using special production processes to reduce density. The composition of mullite insulating bricks is similar to that of mullite bricks, but differences in production processes and microstructure result in superior insulation performance.
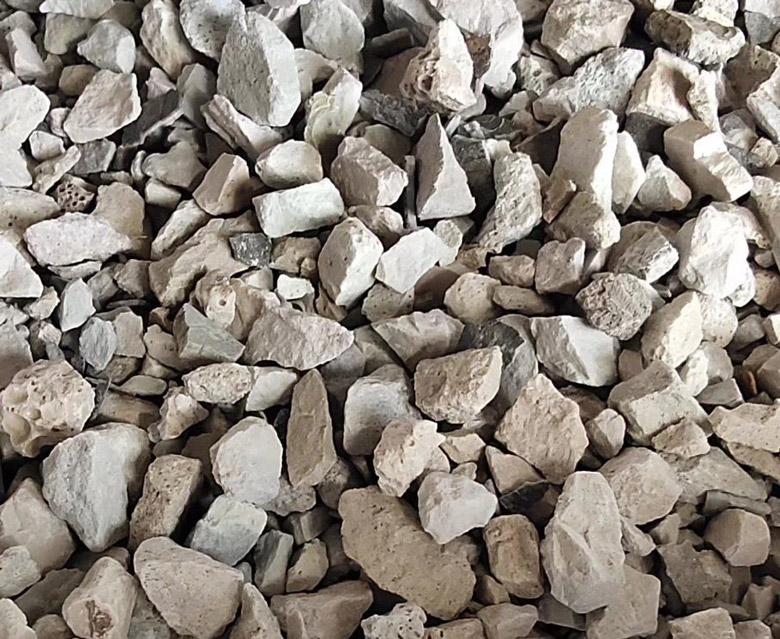
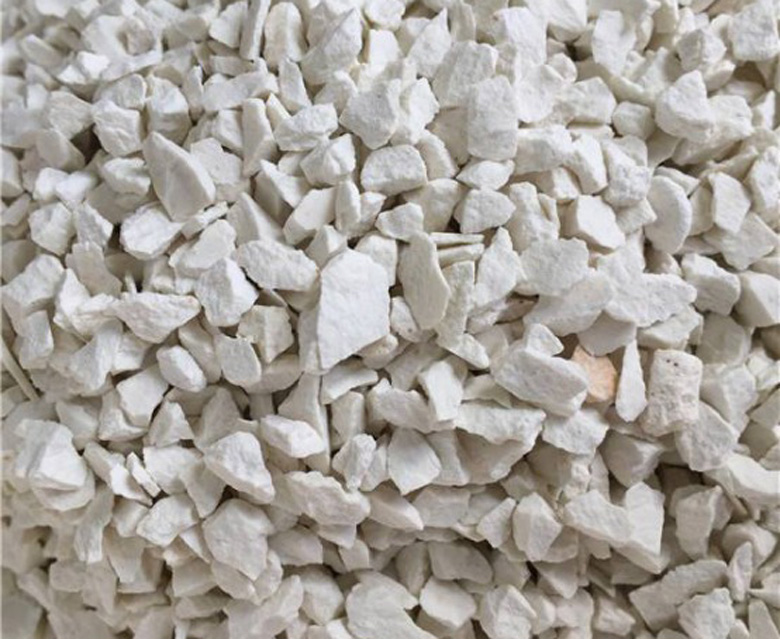
2. Performance Characteristics
Mullite Bricks: These have a refractoriness of over 1790°C, with a load softening temperature typically between 1600°C and 1700°C. The compressive strength at room temperature generally ranges from 70 to 260 MPa.
Mullite Insulating Bricks: These can achieve a refractoriness of over 1800°C and provide excellent thermal insulation, allowing for a significant reduction in furnace wall thickness. Additionally, their lower density effectively reduces the weight of the furnace body. Due to the outstanding insulation performance of mullite insulating bricks, they are widely used in industrial kilns that require efficient insulation, such as hot blast stoves and glass crucibles.
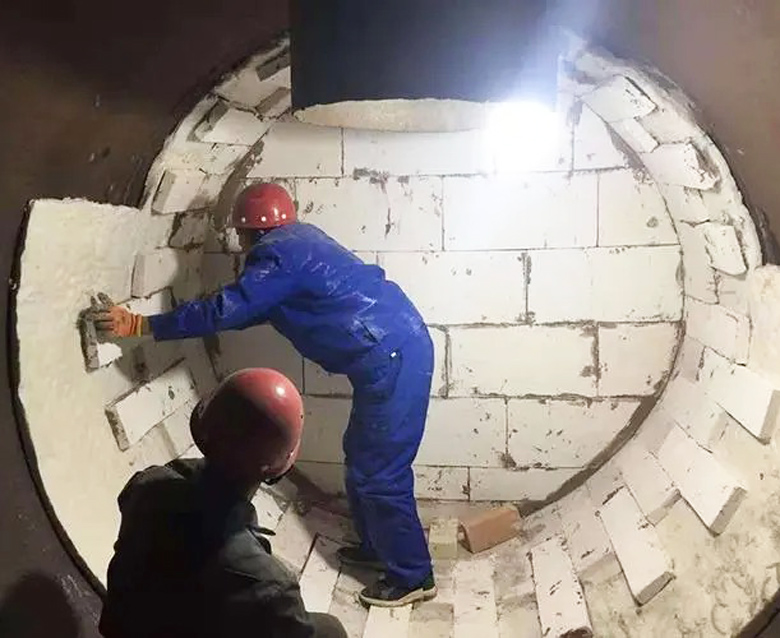
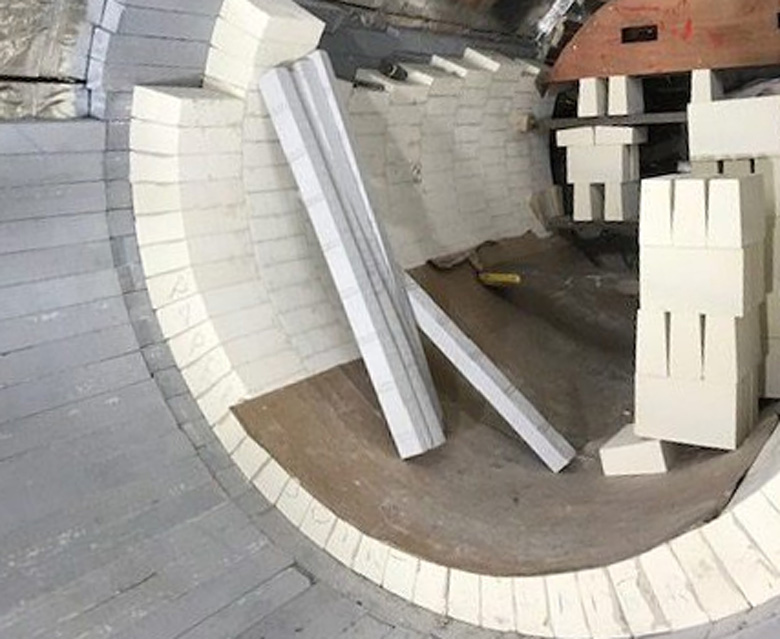
3. Production Process
Mullite Bricks: There are primarily two production methods: sintering and electric melting. Sintered mullite bricks are made using high-alumina bauxite clinker as the main raw material, with a small amount of clay or raw bauxite added as a binder. The mixture is then shaped and fired to create the bricks. Electric melted mullite bricks, on the other hand, use high-alumina materials, industrial alumina, and refractory clay as raw materials, with charcoal or coke fines added as a reducing agent. After shaping, they are produced using the reduction electric melting method.
Mullite Insulating Bricks: These are manufactured using special production processes, such as introducing pores, foam methods, adding burn-out additives, or gasification methods, to reduce density and enhance insulation performance.
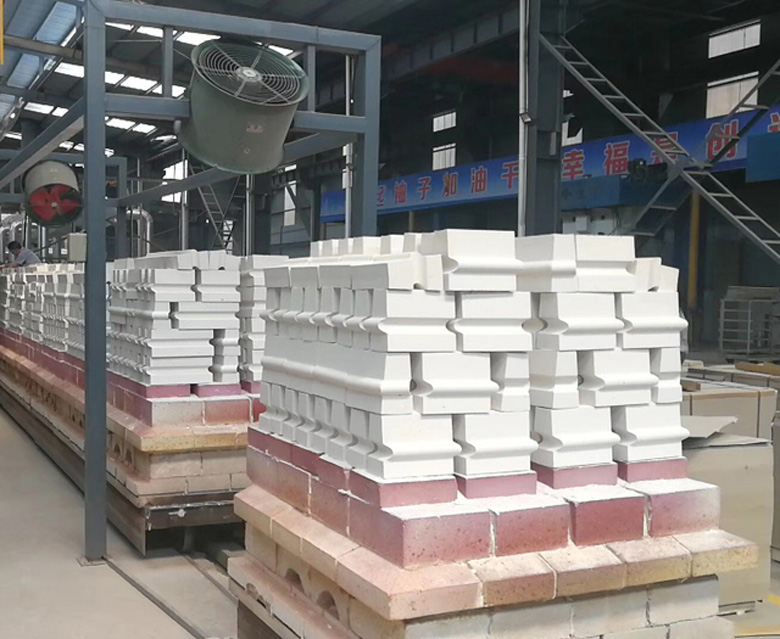
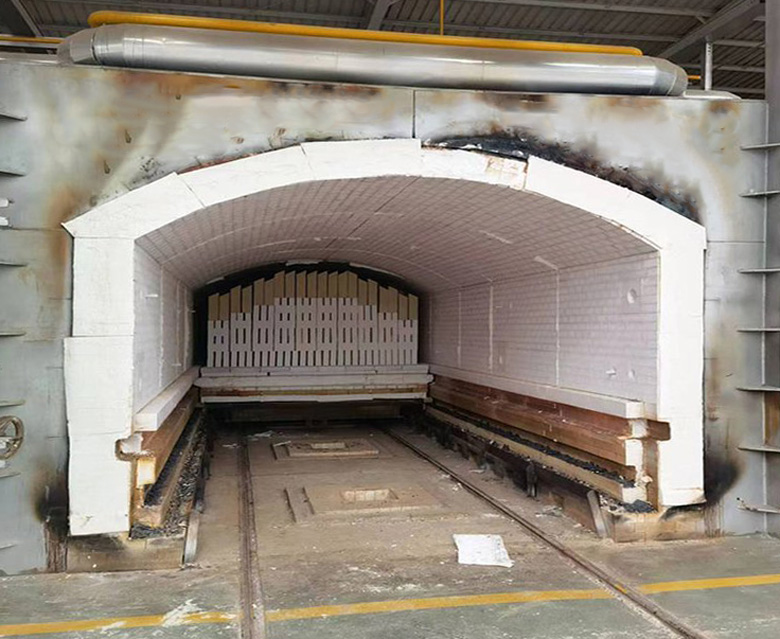
4. Construction Process
Compared to mullite bricks, mullite insulating bricks possess a superior low thermal conductivity, providing excellent thermal insulation effects. This characteristic makes their energy-saving benefits particularly evident during intermittent operations.
Due to the low density, special processes, and excellent performance under high temperature and pressure of mullite insulating bricks, the amount of refractory mortar used can be reduced during application, ensuring the strength and stability of the masonry and extending the service life of the lining.
The Need for Mullite Bricks and Mullite Insulation Bricks
Kerui has been deeply engaged in refractory materials for many years and is an experienced manufacturer and supplier. We can develop targeted application solutions based on your needs and produce mullite insulating bricks in the required dimensions and shapes. These mullite insulating bricks are suitable for various high-temperature environments such as the roofs of hot blast stoves, the bodies and bottoms of blast furnaces, regenerative chambers of glass melting furnaces, ceramic sintering kilns, and dead corner linings in petroleum cracking systems.
If you have any needs related to mullite insulating bricks or refractory materials, please contact us. Kerui will provide prompt service, develop a comprehensive delivery plan, and offer you high-quality refractory materials at competitive factory prices.