In industry, aluminum is widely used in many fields such as automotive, aerospace, construction, electricity, and so on. Therefore, in nonferrous metal production, aluminum production is more than any other metal. The development of the aluminum industry also has a positive impact on promoting scientific and technological progress.
Introduction of Aluminum Industry
Aluminum production is mainly divided into two steps. Firstly, prepare industry alumina. Secondly, use molten salt electrolysis to produce aluminum. In the production process, the high-temperature furnaces include rotary kilns, molten-salt containers, aluminum melting furnaces, and so on. The aluminum industry mainly uses high-temperature equipment to produce aluminum. So the demand for refractory materials is large in the aluminum industry.
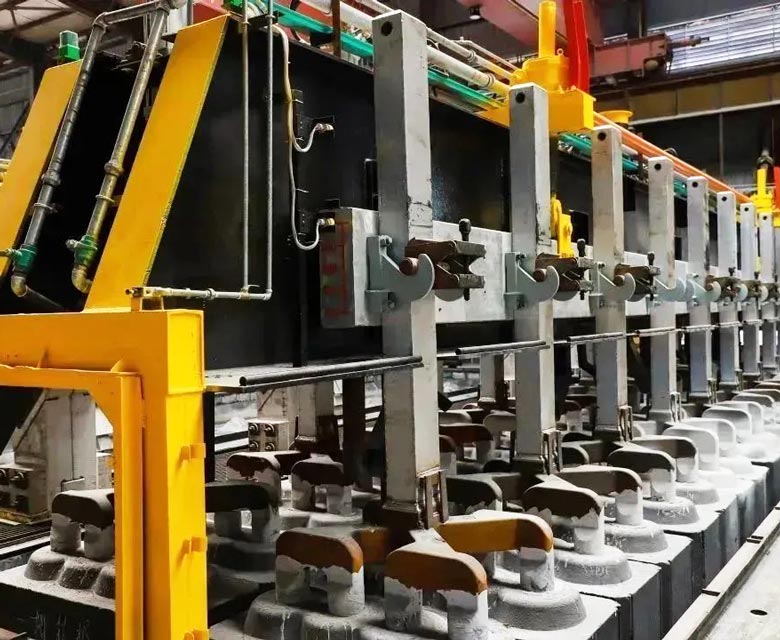
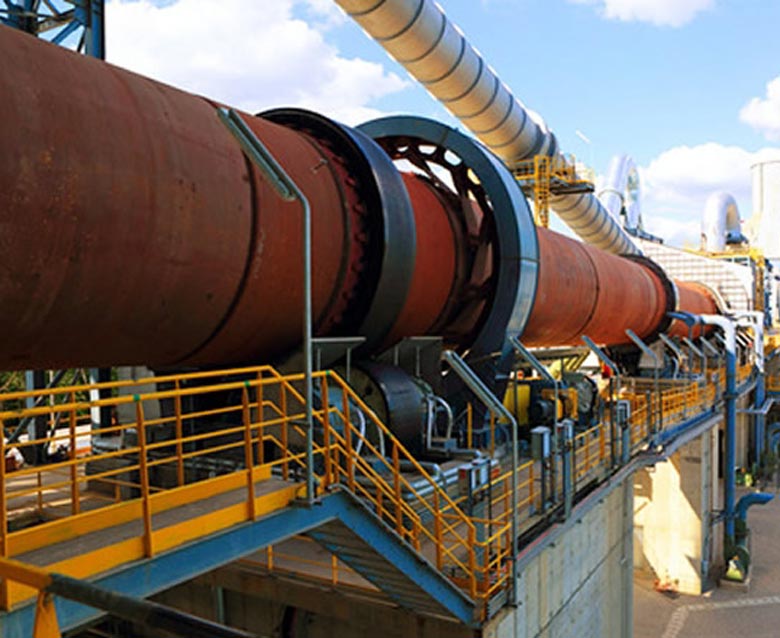
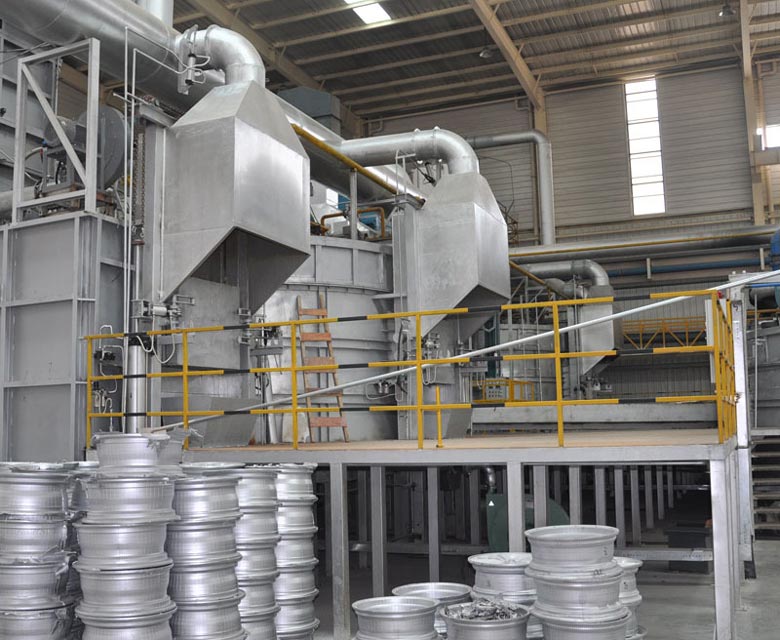
Usages of Refractory Materials in the Aluminum Industry
Rotary kilns usually use high alumina bricks and magnesia chrome bricks as the linings. They have good chemical resistance, thermal and mechanical shock resistance, and great refractoriness in long working time. Besides, the outlets of rotary kilns usually use refractory castable.
Molten-salt containers require refractory materials with good electrical conductivity and chemical resistance in high-temperature environments. It usually uses carbon bricks and silicon nitride bonded silicon carbide bricks. The reason is that they will not react with aluminum solutions. In this situation, the equipment can keep a stable state to extend the life cycle.
Aluminum melting furnaces will release alkaline gas. So the refractory materials need to have good chemical resistance and thermal shock resistance. The linings of aluminum melting furnaces usually use high alumina bricks, mullite bricks, and corundum bricks. The vulnerable parts use silicon nitride bonded silicon carbide bricks. Fire clay bricks can be used in the linings that indirectly contact the solutions.