The iron and steel smelting industry has a huge demand for refractory materials. This industry accounts for almost 75% of the consumption of refractory materials. Most refractories are used in processes such as metal smelting, melting, casting, etc. Kerui Refractory has extensive experience in this industry. We can provide customized one-stop solutions for partners’ needs in the steel industry, including kiln solution design, refractory material optimization solutions, construction solutions, after-sales service, etc.
Introduction of Iron & Steel Industry
In recent years, the steel industry has been developing rapidly. It is the foundation industry of the national economy. It complements urbanization and industrialization. Therefore, the steel industry is crucial for the development of every country.
China is the largest producer and consumer of iron & steel. The country has a mature and advanced steel production system. In order to improve the efficiency and safety of steel industry production, iron and steel plants are equipped with corresponding high-performance refractory products. These refractory products can improve the service life of steel production equipment and save energy efficiency.
There are many types of refractory materials. When partners in the iron and steel industry need to choose refractory materials, please contact Zhengzhou Kerui (Group) Refractory Co., Ltd.. We will provide detailed refractory material solutions for the steel industry construction according to the partner’s requirements.
Kerui Provides Refractory Materials Solutions for Steel & Iron Factories
Refractory materials are widely used in many factories in the steel industry. They are often applied in these fields:
- Steel Plant
- Iron Plant
- Steel Rolling Mill
- Special Steel Plant
- Iron & Steel Plate Mill
- Iron & Steel Pipe Mill and Other Factories.
Besides, Kerui also offers mullite castable, chrome corundum brick and other kinds of refractory materials.
Applications of Refractory in the Iron & Steel Industry
Refractory materials are used in various equipment in the steel industry. In the furnaces, these refractory materials are mainly used in the throat, body, waist, top, bottom, hearth, tuyere, iron outlet, chimney, pipe, etc.
According to the production process, the primary applications of refractories in the steel industry can be categorized into three main areas:
- Part 1 Ironmaking and Steelmaking
- Part 2 External Refining
- Part 3 Continuous Casting
Part 1 Ironmaking and Steelmaking
Usually, blast furnaces and hot blast furnaces are used for ironmaking. Converters, open hearth furnaces, and electric arc furnaces are used for steelmaking.
Blast Furnace
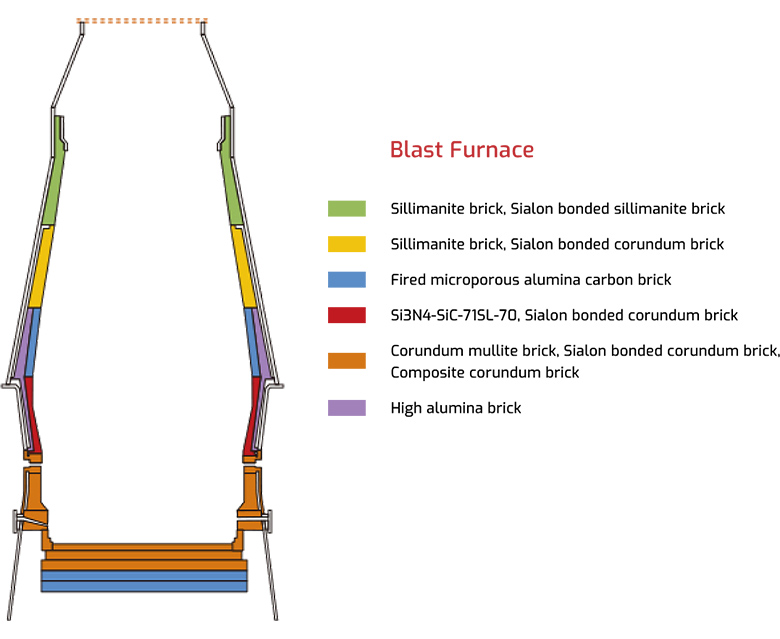
- Upper part of the furnace: Clay bricks.
- Middle part of the furnace: Alumina refractory bricks, corundum bricks.
- From the throat to the upper part of the furnace: Aluminosilicate materials, high-alumina bricks, dense clay bricks or SiC bricks.
- Middle and lower part of the furnace body, furnace waist and furnace belly: Clay bricks, high alumina bricks, corundum bricks, Si3N4 bonded SiC bricks, hot-pressed semi-graphite bricks, silicon line bricks, aluminum-carbon bricks, semi-graphite carbon-SiC bricks, Sialon bonded SiC bricks.
- Furnace hearth and furnace bottom: Baked carbon bricks, hot-pressed carbon bricks, microporous carbon bricks, super microporous carbon bricks, C-SiC bricks, semi-graphitized self-baked carbon blocks, corundum-mullite bricks, corundum bricks.
- Blast furnace lining repair and maintenance: Aluminum carbide silicon spray repair material, clay spray repair material, high alumina castable, aluminum carbon ramming material.
- Iron outlet (cast-house): Aluminum carbide silicon carbon castable.
Hot Blast Furnace
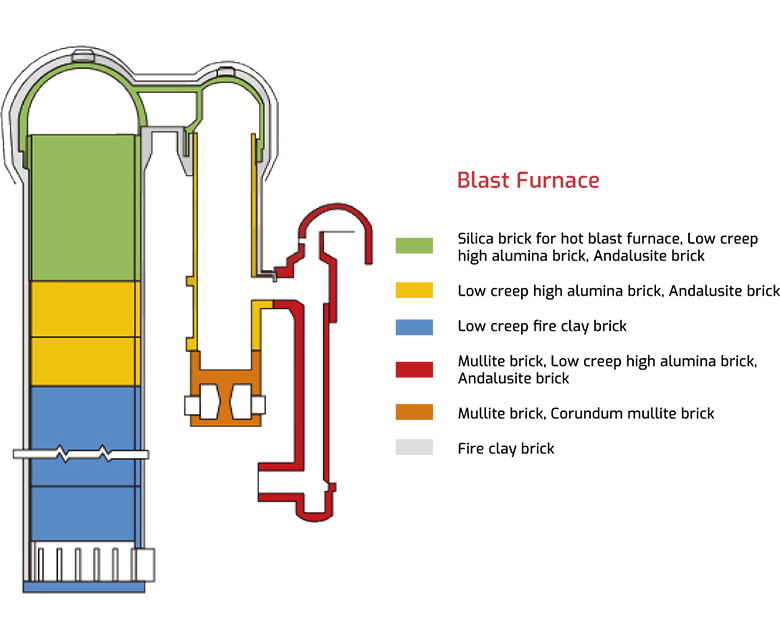
- Hot blast stove: Dense clay castable, heat shock resistant castable, aluminosilicate refractory mortar, high alumina refractory mortar, anti-creep high alumina brick, low creep silicon brick, sillimanite brick, sintered mullite brick, andalusite brick, clay brick.
Converter
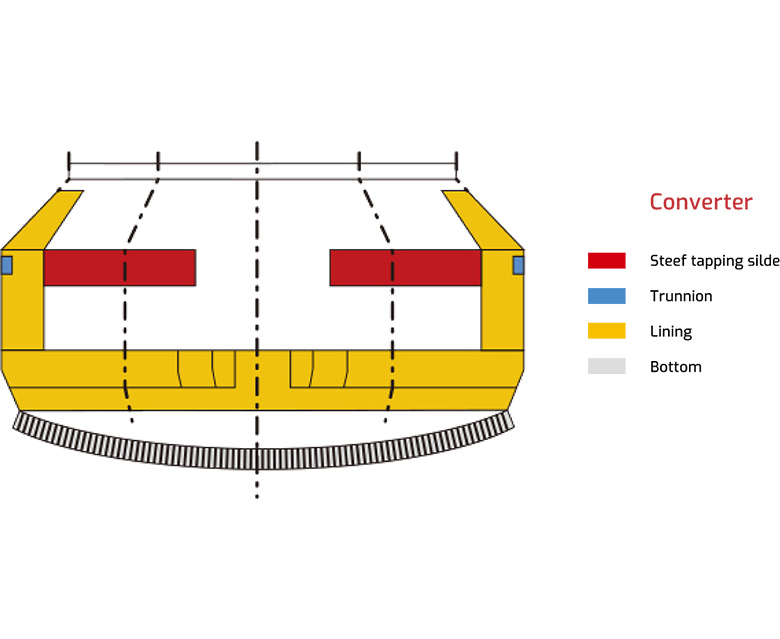
- Insulation layer: Polycrystalline refractory fiber.
- Permanent layer: Magnesium carbon bricks, tar dolomite bricks, sintered magnesia bricks.
- Steel outlet of converter: Magnesia carbon bricks.
- Furnace bottom: Magnesia carbon bricks.
- Converter furnace edge: Magnesia ramming mass.
Open Hearth Furnace
- Melting pool in the melting chamber: Clay refractories, magnesia bricks, high-magnesia synthetic mortar, high-iron synthetic mortar, dry magnesia sand spraying.
- Furnace walls in the melting chamber: Magnesia bricks, magnesia cement, high-alumina bricks.
- Furnace roof in the melting chamber: Magnesia-chrome bricks, periclase-spinel bricks, magnesia aluminum bricks, magnesia alumina chrome bricks.
- Furnace head and riser in the melting chamber: Magnesia bricks, magnesia aluminum bricks, magnesia chrome bricks, aluminosilicate ceramic fiber blankets.
- Slag chamber and heat storage chamber: Magnesia aluminum bricks, high alumina bricks, alkaline bricks, clay bricks, checker bricks, magnesia olivine checker bricks.
- Flue and chimney: Clay bricks, castable refractory material.
Electric Furnace
- Furnace roof: High alumina bricks, precast refractory blocks.
- Electrode triangle area of the furnace roof: Chrome corundum and corundum magnesia refractory castable and precast blocks.
- Outer perimeter roof of the furnace: High-alumina bricks, magnesia bricks, magnesia chrome bricks, etc.
- Tapping spout: Unshaped ramming material and precast refractory concrete (high-alumina, magnesia), magnesia-carbon bricks, silicon carbide bricks.
- Furnace wall: Direct-bonded magnesia chrome bricks, pre-reacted magnesia-chrome bricks, magnesia bricks.
- Slag line and hot spot: Oil-impregnated magnesia bricks, direct-bonded magnesia chrome bricks, fused-cast magnesia chrome bricks, magnesia carbon bricks.
- Furnace cover: High alumina refractory castable, mullite refractory castable, corundum refractory castable, chrome corundum refractory castable.
- Furnace bottom: Sintered magnesia carbon bricks, magnesia carbon ramming mass, insulating bricks, sintered magnesia mortar, asphalt-bonded magnesia bricks, magnesia calcium iron mortar.
- Iron ladle and ladle car: Dense clay bricks, mullite bricks, magnesia bricks, magnesia aluminum bricks, silicon carbide bricks, refractory castable.
Part 2 External Refining
Ladle refining refers to a metallurgical process where the steel liquid initially refined in a converter, open-hearth furnace, or electric furnace is transferred to another container for further refining. This includes degassing, deoxidation, desulfurization, removal of inclusions, and fine-tuning of components. This process consists of six parts, including AOD Refining Furnace, RH Refining Furnace, RH furnace, LF furnace, LF furnace, VOD furnace.
AOD Refining Furnace
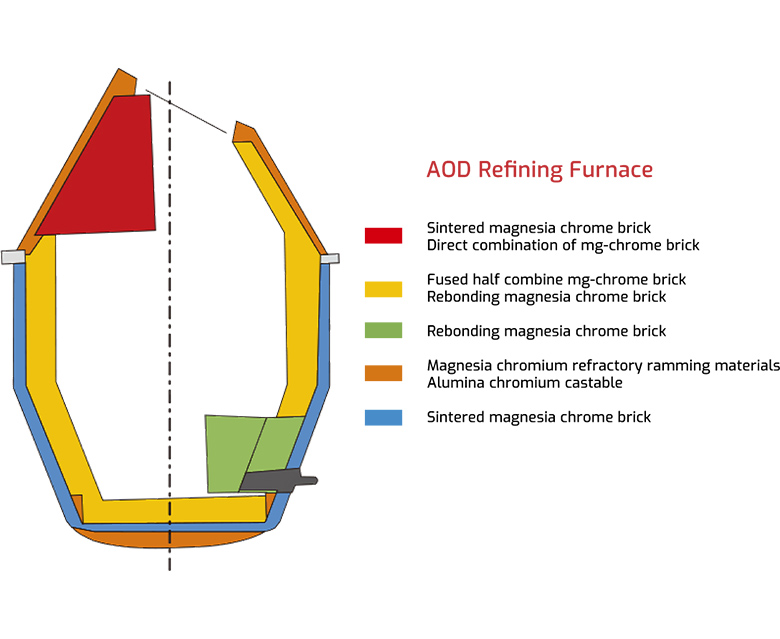
- Furnace cap: Chrome magnesite bricks, High alumina plastic refractories, Asphalt-bonded magnesite bricks, and others.
- Furnace wall: Dolomite bricks, and others.
- Furnace lining: Direct-bonded magnesia chrome bricks, Rebonded magnesia chrome bricks, Semi-rebonded magnesia chrome bricks, and others.
- Furnace bottom: Magnesia dolomite bricks, and others.
- Tuyere bricks: High-purity direct-bonded and rebonded magnesia chrome bricks, ultra-high-temperature sintered dolomite bricks, electrically fused dolomite bricks, and others.
RH Refining Furnace
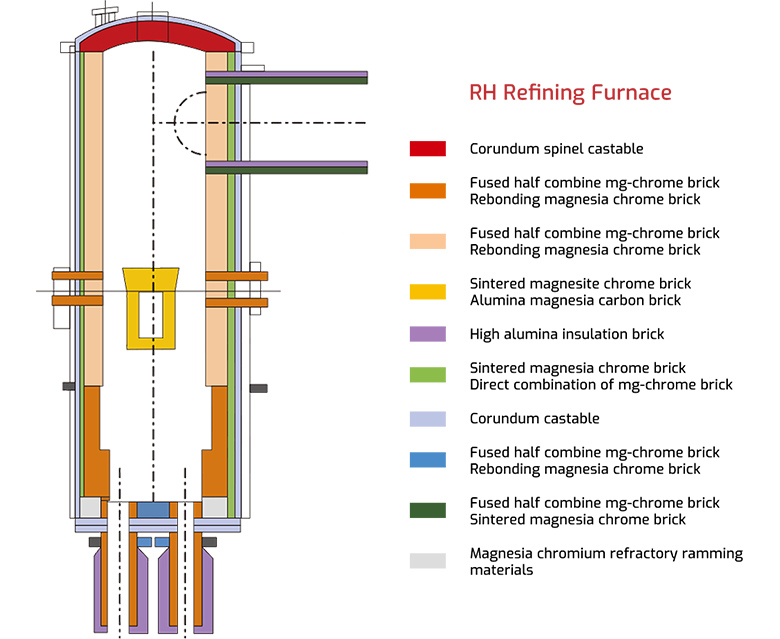
- Vacuum chamber: Direct-bonded magnesia chrome bricks, Magnesia chrome bricks, High alumina bricks, and others.
- Ascending pipe: High alumina bricks, and others.
- Descending pipe: High alumina bricks, and others.
- Ordinary ladle: Magnesia carbon bricks, aluminum magnesia carbon bricks, aluminum magnesia refractory castable, corundum spinel refractory castable, corundum refractory castable, chrome corundum refractory castable, spinel refractory castable, magnesia refractory castable.
LF Furnace
- Ladle wall, ladle bottom, and slag line: Magnesia aluminum carbon bricks, magnesia carbon bricks, magnesia calcium bricks, magnesia chrome bricks, magnesia zircon refractory castable, zircon mullite bricks, spinel refractory castable, and others.
ASEA-SKF Furnace
- Slag line: Magnesia carbon bricks, magnesia chrome bricks, magnesia bricks, magnesia dolomite bricks, high alumina bricks, and others.
- Measuring wall and ladle bottom: High-alumina bricks, refractory castable, aluminum carbon bricks, and others.
VOD Furnace
- Sidewalls and ladle bottoms: Direct-bonded magnesia chrome bricks, semi-rebonded magnesia chrome bricks, and others.
- Slag line: Rebonded magnesia chrome bricks, semi-rebonded magnesia chrome bricks, high calcium magnesia dolomite bricks, magnesia dolomite bricks, and others.
Part 3 Continuous Casting
Continuous casting is the process of continuously producing ingots by taking measures of forced cooling while the molten steel is in motion. This process involves four equipment, including ladle and tundish, steel ladle sliding gate system.
Ladle and Tundish
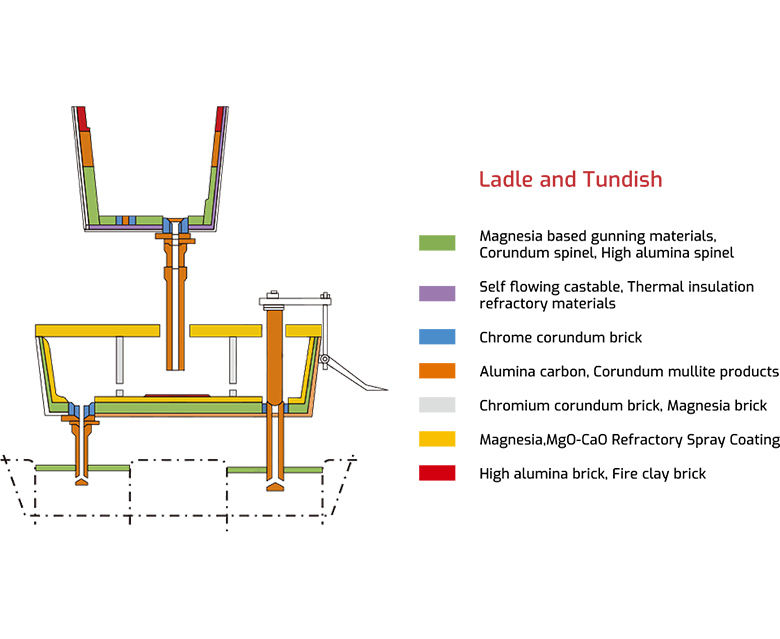
- Insulation layer: Ceramic fiber insulation boards, Insulating bricks, lightweight refractory castable, and others.
- Permanent layer: Clay bricks, mullite refractory castable, High-alumina refractory castable, and others.
- Working layer: Dry-vibrated material.
- Stool bricks: High-alumina bricks, corundum bricks, and others.
- Ladle bottom: The same as the working layer.
- Impact zone: Magnesia precast blocks, corundum precast blocks, and others.
- Dam wall: Magnesia aluminum dams, magnesia dams, and others.
- Steel purification filter: Mullite material, corundum material, calcium oxide material, refractory fibers, porous alumina ceramic tubes, and others.
- Intermediate ladle cover.
Torpedo Car
- Torpedo ladle spout: Corundum mullite refractory castable, and others.
- Torpedo ladle body: High alumina refractory castable, and others.
- Torpedo ladle: Coating material, and others.
Steel Ladle Sliding Spout System
- Steel ladle upper and lower spout bricks: High alumina bricks, corundum bricks, aluminum bricks
- Sliding plate bricks: Magnesia bricks, zirconia bricks, aluminum carbon bricks, magnesia carbon bricks.
- Intermediate ladle sliding spout: Aluminum zirconium carbon bricks, mullite upper spout, composite spout, and others.
- Sliding plate: Magnesia spinel materials, aluminum carbon materials, zirconia materials, and others.
- Fixed spout size nozzle: Zirconia materials, and others.
Continuous Casting Main Components
- Shroud: Fused silica products, Aluminum carbon materials, and others.
- Stopper: Aluminum carbon materials, and others.
- Submerged nozzles: Fused silica nozzles, Aluminum carbon materials.
NOTE: The above Kerui Refractory only showcases a portion of the kiln solutions. These solutions are for reference only.
Which Refractory Materials Are Used in the Iron & Steel Industry?
Kerui Refractory typically provides several types of refractory products for use in the steel industry, including shaped refractory materials, unshaped refractory materials, ceramic fiber products, and so on. These products have different applications and locations. We can provide you with a complete kiln refractory construction solution to achieve high production in your steel industry. Kerui Refractory can also customize refractory products to meet the specific requirements of partners for special applications.
– Shaped refractory materials include various refractory bricks and various insulation bricks. These standard bricks have fixed shapes, sizes, and compositions.
They include sillimanite brick, alumina carbon brick, corundum-mullite brick, corundum brick, high-alumina brick, clay brick, alumina carbon brick, andalusite brick, magnesia brick, silica brick, chrome corundum brick, rebonded magnesia chrome brick, high alumina insulation brick, magnesia chrome brick, etc.
– Unshaped refractory materials contain refractory cement, refractory mortar, refractory ramming material, refractory castable, refractory precast shapes, and so on. These refractory materials can be processed into any shape after construction to meet application requirements.
These unshaped materials include clay castable, high alumina castable, high alumina refractory cement, chrome corundum castable, corundum castable, magnesia chrome ramming mass, etc.
One Stop Solution of Refractory Materials for Steel Iron Industry
Kerui Refractory can provide partners with a one-stop refractory kiln solution, including selecting refractory materials to implementing and operating kiln solutions. We have rich experience and strong production capabilities in this industry. Please contact us to customize your exclusive refractory solution.